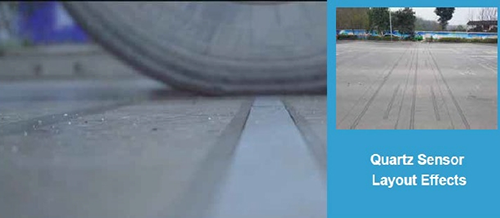
1. التكنولوجيا الأساسية
حاليًا، تُستخدم أنظمة إدارة حركة المواد (WIM) القائمة على مستشعرات وزن الكوارتز الكهرضغطية على نطاق واسع في مشاريع مثل مراقبة الحمل الزائد للجسور والقنوات، وتطبيق نظام مراقبة الحمل الزائد خارج الموقع لمركبات الشحن على الطرق السريعة، والتحكم التكنولوجي في الحمل الزائد. ومع ذلك، لضمان الدقة وعمر الخدمة الطويل، تتطلب هذه المشاريع إعادة بناء رصف الخرسانة الأسمنتية في منطقة تركيب مستشعرات وزن الكوارتز الكهرضغطية باستخدام أحدث التقنيات. ولكن في بعض بيئات التطبيق، مثل أسطح الجسور أو الطرق الرئيسية الحضرية ذات الضغط المروري الكثيف (حيث يكون وقت تصلب الأسمنت طويلًا جدًا، مما يُصعّب إغلاق الطرق لفترات طويلة)، يصعب تنفيذ هذه المشاريع.
السبب في عدم إمكانية تركيب مستشعرات الوزن الكهرضغطية المصنوعة من الكوارتز مباشرةً على الرصيف المرن هو: كما هو موضح في الشكل 1، عند مرور العجلة (خاصةً تحت حمولة ثقيلة) على الرصيف المرن، يكون سطح الطريق منخفضًا نسبيًا. ومع ذلك، عند الوصول إلى منطقة مستشعر الوزن الكهرضغطي الصلب المصنوع من الكوارتز، تختلف خصائص انخفاض المستشعر عن منطقة واجهة الرصيف. علاوة على ذلك، يفتقر مستشعر الوزن الصلب إلى الالتصاق الأفقي، مما يتسبب في انفصاله السريع عن الرصيف.
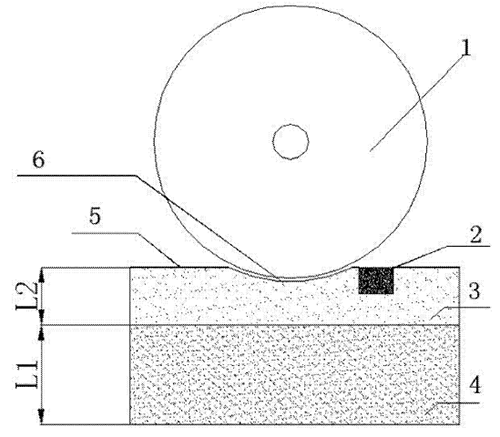
(1 عجلة، 2 مستشعر وزن، 3 طبقة أساسية ناعمة، 4 طبقة أساسية صلبة، 5 رصيف مرن، 6 منطقة هبوط، 7 وسادة رغوية)
بسبب اختلاف خصائص الهبوط واختلاف معاملات احتكاك الرصيف، تتعرض المركبات التي تمر عبر مستشعر الوزن الكوارتزي الكهرضغطي لاهتزازات شديدة، مما يؤثر بشكل كبير على دقة الوزن الإجمالية. بعد ضغط المركبة لفترات طويلة، يكون الموقع عرضة للتلف والتشقق، مما يؤدي إلى تلف المستشعر.
2. الحل الحالي في هذا المجال: إعادة بناء رصف الأسمنت والخرسانة
نظرًا لصعوبة تركيب مستشعرات وزن الكوارتز الكهرضغطية مباشرةً على الرصف الإسفلتي، فإن الإجراء المُتبع في هذا القطاع هو إعادة بناء رصف خرساني أسمنتي لمنطقة تركيب مستشعرات وزن الكوارتز الكهرضغطية. يتراوح طول إعادة البناء عادةً بين 6 و24 مترًا، بعرضٍ مُساوٍ لعرض الطريق.
على الرغم من أن إعادة بناء رصف الخرسانة الأسمنتية تلبي متطلبات القوة لتثبيت أجهزة استشعار الوزن الكوارتزية الكهرضغطية وتضمن عمر الخدمة، إلا أن العديد من القضايا تحد بشدة من الترويج لها على نطاق واسع، على وجه التحديد:
1) تتطلب عملية إعادة بناء الرصيف الأصلي باستخدام الأسمنت المكثف كمية كبيرة من تكاليف البناء.
٢) يتطلب إعادة بناء الخرسانة الأسمنتية وقتًا طويلًا للغاية. تستغرق فترة تصلب رصف الأسمنت وحده ٢٨ يومًا (وهو متطلب قياسي)، مما يؤثر بلا شك بشكل كبير على تنظيم حركة المرور. خاصةً في بعض الحالات التي تتطلب أنظمة إدارة حركة المرور (WIM) مع وجود تدفق مروري كثيف في الموقع، غالبًا ما يكون بناء المشروع صعبًا.
3) تدمير البنية التحتية الأصلية للطريق، مما يؤثر على المظهر.
4) يمكن أن تؤدي التغييرات المفاجئة في معاملات الاحتكاك إلى ظاهرة الانزلاق، وخاصة في الظروف الممطرة، مما قد يؤدي بسهولة إلى وقوع الحوادث.
5) تؤدي التغييرات في بنية الطريق إلى اهتزازات المركبة، مما يؤثر على دقة الوزن إلى حد ما.
6) لا يمكن تنفيذ إعادة بناء الخرسانة الأسمنتية على بعض الطرق المحددة، مثل الجسور المرتفعة.
٧) حاليًا، يتجه قطاع المرور نحو التحول من الأبيض إلى الأسود (تحويل رصف الإسمنت إلى رصف أسفلتي). الحل الحالي هو التحول من الأسود إلى الأبيض، وهو ما يتعارض مع المتطلبات ذات الصلة، وغالبًا ما تكون وحدات البناء مقاومة.
3. محتوى مخطط التثبيت المُحسَّن
الغرض من هذا المخطط هو حل مشكلة عدم القدرة على تركيب أجهزة استشعار الوزن الكهرضغطية الكوارتزية مباشرة على رصف الأسفلت الخرساني.
يُثبّت هذا النظام مُستشعر وزن الكوارتز الكهرضغطي مباشرةً على طبقة القاعدة الصلبة، مما يُجنّب مشكلة عدم التوافق طويل الأمد الناتجة عن دمج هيكل المستشعر الصلب مباشرةً في الرصيف المرن. يُطيل هذا من عمر الخدمة بشكل كبير ويضمن دقة الوزن دون التأثير على جودته.
علاوة على ذلك، ليست هناك حاجة لإجراء إعادة بناء رصف الخرسانة الأسمنتية على رصف الأسفلت الأصلي، مما يوفر كمية كبيرة من تكاليف البناء ويقصر فترة البناء بشكل كبير، مما يوفر إمكانية الترويج على نطاق واسع.
الشكل 2 هو مخطط تخطيطي للهيكل مع مستشعر الوزن الكوارتز الكهرضغطي الموضوع على الطبقة الأساسية الناعمة.
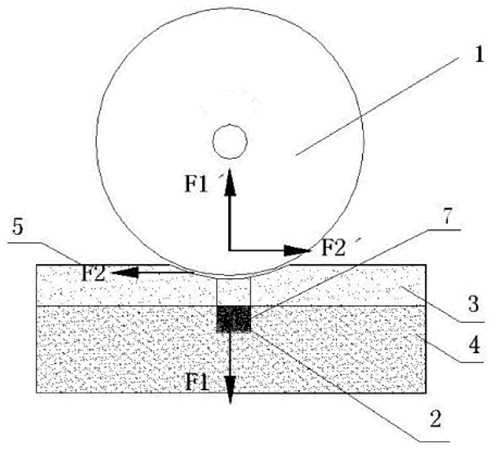
(1 عجلة، 2 مستشعر وزن، 3 طبقة أساسية ناعمة، 4 طبقة أساسية صلبة، 5 رصيف مرن، 6 منطقة هبوط، 7 وسادة رغوية)
4. التقنيات الرئيسية:
1) حفر مسبق لقاعدة الهيكل لإنشاء فتحة إعادة البناء، بعمق فتحة 24-58 سم.
٢) تسوية قاع الفتحة وصب مادة الحشو. تُسكب نسبة ثابتة من رمل الكوارتز + رمل الفولاذ المقاوم للصدأ وراتنج الإيبوكسي في قاع الفتحة، وتُملأ بالتساوي، بعمق حشو يتراوح بين ٢ و٦ سم، وتُسوى.
٣) صبّ طبقة القاعدة الصلبة وتركيب مستشعر الوزن. صبّ طبقة القاعدة الصلبة وثبّت مستشعر الوزن فيها، باستخدام وسادة إسفنجية (٠.٨-١.٢ مم) لفصل جوانب مستشعر الوزن عن طبقة القاعدة الصلبة. بعد تصلب طبقة القاعدة الصلبة، استخدم آلة طحن لطحن مستشعر الوزن وطبقة القاعدة الصلبة حتى يصبحا على نفس المستوى. يمكن أن تكون طبقة القاعدة الصلبة صلبة، أو شبه صلبة، أو مركبة.
٤) صب الطبقة السطحية. استخدم مادةً متوافقةً مع طبقة الأساس المرنة لصب وملء الارتفاع المتبقي من الفتحة. أثناء عملية الصب، استخدم آلة ضغط صغيرة للضغط ببطء، مع ضمان استواء السطح المُعاد بناؤه مع أسطح الطرق الأخرى. الطبقة الأساسية المرنة هي طبقة سطحية من الأسفلت الحبيبي متوسط إلى ناعم.
5) نسبة سمك الطبقة الأساسية الصلبة إلى الطبقة الأساسية المرنة هي 20-40:4-18.
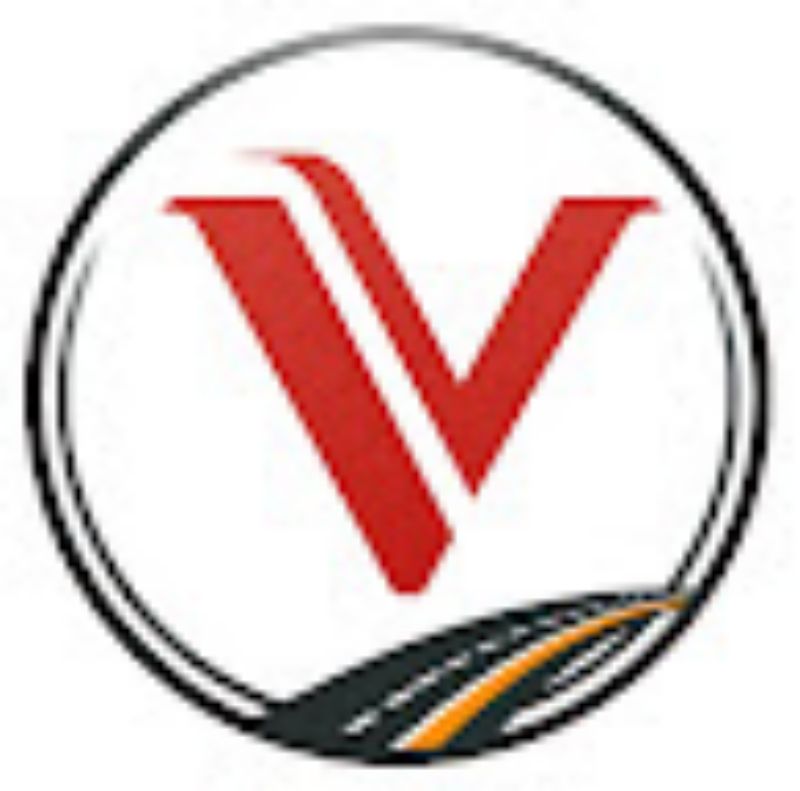
شركة إنفيكو للتكنولوجيا المحدودة
E-mail: info@enviko-tech.com
https://www.envikotech.com
مكتب تشنغدو: رقم 2004، الوحدة 1، المبنى 2، رقم 158، شارع تيانفو الرابع، المنطقة التكنولوجية المتقدمة، تشنغدو
مكتب هونج كونج: الطابق الثامن، مبنى تشيونج وانج، شارع سان ووي رقم 251، هونج كونج
المصنع: المبنى 36، المنطقة الصناعية جينجيالين، مدينة ميانيانغ، مقاطعة سيتشوان
وقت النشر: ٨ أبريل ٢٠٢٤